Method Matters
Before welding can begin, a method is chosen. Equipment and base metals are measured, positioned and prepped. Long before a project begins, the welder is trained and prepared. The art of welding comes from a welder’s personal method and procedure. Many variables affect the characteristic a weld. Though each welder will not be able to replicate the exact same weld as his or her peers, a standard quality must be maintained.
Standard Procedures for Consistency
Procedure qualification records (PQRs) ensure a sound weld in specific situations. Welders have unique approaches to balancing the variables of welding. Material, thickness, type of joint, and angle of weld all must be considered. Heat must be kept even between the two workpieces to maintain consistency. A welder with a positive record can successfully weld in a variety of situations; mastery of these situations allows development of personal style.
Avoiding Contamination
Atmospheric contamination is an utmost concern to welders. If a weld is done without proper shielding, the result may be porous or weak. Flux is used to coat the electrode in shielded arc welding. Flux is also used to cover the weld area in submerged arc welding. Flux is consumed, creating carbon dioxide and slag. The carbon dioxide acts as a shielding gas and protects the weld, while slag remains as a solid byproduct of melted flux. Slag is removed for quality assurance and aesthetic consistency. MIG and TIG welding use argon gas as a shielding agent. Argon is a non-reactive gas. It protects well against contamination and is supplied by the weld gun. TIG welding often requires high precision—in some applications the workpieces are laced in a small chamber filled with argon gas to provide a “clean room” environment, preventing contamination.
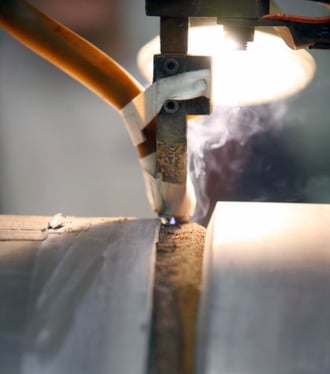
Certifications Assure Quality and Consistency
Certification is a must in the welding industry. Workmanship and continuous quality are the measures of performance for a master welder. Certification is only awarded to welders producing consistent quality work. For fabrication companies to accept projects, they must meet specific codes and hold proper certification—proof of consistent quality work. These measures guarantee only approved welders contribute to projects where accuracy and precision are vital. Holding certificates allows customers, as well as governments, to be ensured of the quality of work they will be receiving. Certifications must be updated; quality and craftsmanship must therefore be maintained.
AT&F holds certifications for a variety of industry specifications and prides itself on maintaining the highest level of excellence from its welding teams.